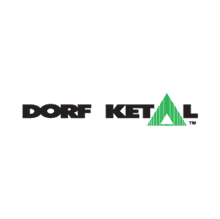 |
Solvent-based flexographic and gravure inks have long been a top choice for printing brand and product information on flexible packaging. When ink is applied to flexible packaging, it is printed on the outermost layer of the package, which serves as a print-receptive layer for the ink. This layer can be made from plastics such as polyethylene, polypropylene, or polyester. |
Since this outermost layer can be subjected to various environmental conditions and rough handling situations during the package’s lifespan, it is important to ensure the ink applied adheres well and forms a strong film. It is also essential for the ink to cure quickly to various types of plastic films to optimize the efficiency of flexible packaging manufacturing. Given this, solvent-based ink formulators require an additive that maximizes durability and efficiency to offer the best value for their customers.
Tyzor® Titanates
For over 40 years, Dorf Ketal’s Tyzor® titanates have played an instrumental role as additives that improve the physical properties and performance of various coating, ink, and adhesive systems used across several industries. In general, adding Tyzor® to printing ink formulations imparts the following performance improvements:
- Increased ink adhesion
- Enhanced resistance to heat, chemicals, solvents, and water
- Reduction of drying times or a decrease in cure temperature
Solvent-based flexographic and gravure printing ink formulations typically used in flexible packaging contain binders such as
cellulose acetate butyrate,
cellulose acetate propionate, polyvinyl butyral, or nitrocellulose. These binders, as well as pigments in the formulation, contain hydroxyl or carboxyl functional groups that react with Tyzor® additives to facilitate cross-linking and adhesion promotion, as shown below.
Adhesion to plastic substrates made of polyethylene and polypropylene is difficult because of a lack of functional groups. Since Tyzor® additives require hydroxyl or carboxyl groups to promote adhesion, films made of such plastics must be pretreated with corona, flame, or plasma.
Traditionally, titanium acetylacetonates were titanate additives used in printing ink formulations to cross-link and promote adhesion. These additives provide excellent adhesion to treated polypropylene. To demonstrate, the
Tyzor® AA-75 additive was added to an ink at 2% to compare ink removal by an adhesive tape. As shown below, Tyzor® AA-75 significantly improved adhesion and resisted delamination from the substrate throughout the different stages of the test.
When considering ink applications, however, titanium acetylacetonate additives may release acetylacetone during the curing process and contribute to odor issues if the acetylacetone migrates through the ink substrate. Additionally, titanium acetylacetonates can potentially cause discoloration when used in certain ink binder systems. Therefore, a titanate additive that improves ink adhesion, durability, and efficiency while preventing these issues in ink systems is necessary.
Tyzor® IAM
Dorf Ketal developed
Tyzor® IAM to help overcome the drawbacks listed above while offering the valuable performance improvements of titanate additives in ink applications. When used in solvent-based printing ink formulations, Tyzor® IAM contributes the following properties:
- High stability in solvent-based ink formulations and high reactivity during curing
- Excellent adhesion promotion and cross-linking
- Improved resistance to water, solvents, chemicals, and heat
- Low to no discoloration in ink films
- Fast solvent release during curing
- No release of acetylacetone
- Effective at low concentrations ranging from 1% to 4%
Tests were conducted to compare the efficacy of Tyzor® IAM against Tyzor® AA-75 in terms of adhesion performance, solvent and water resistance, and discoloration.
Test #1: Adhesion of Ink to OPP Foil
Tyzor® IAM and Tyzor® AA-75 were added in concentrations ranging from 0% to 5% to commercial printing inks based on a nitrocellulose binder. After printing and curing, the adhesion of these inks was measured using a tape pull-off method at 1-, 3-, 5-, 10-, and 30-minute intervals and after 1, 3, 5, and 24 hours. The results were compiled below, where adhesion results were ranked on a scale from 1 to 6, where 1 represents excellent adhesion with no delamination and 6 indicates poor adhesion with full delamination. Tyzor® IAM showed better adhesion than Tyzor® AA-75 when added at concentrations of 2% or greater.
Test #2: Solvent and Water Resistance
In this test, Tyzor® IAM and Tyzor® AA-75 were once again added in varying concentrations to commercial printing inks based on nitrocellulose. These inks were printed and cured, then subjected to 50–50 and 70–30 ethanol–water solutions for 1 minute. Both inks containing either Tyzor® IAM or Tyzor® AA-75 showed high resistance to water and solvents, with no significant difference between them.
Test #3: Discoloration
Discoloration was measured using a spectrophotometer and comparing a basic white ink containing either Tyzor® IAM or Tyzor® AA-75. The degree of discoloration was characterized by evaluating the inks containing Tyzor® versus the ink without Tyzor®, measured as ∆b. The results are below, where a higher ∆b value indicates stronger discoloration than the unmodified ink. From this, it is clear that Tyzor® IAM does not contribute to significant yellowing compared to Tyzor® AA-75.
Tyzor® (Grade, Concentration) |
∆b (65°) |
AA-75, 2% |
0.44 |
IAM, 1% |
0.01 |
IAM, 2% |
0.14 |
IAM, 3% |
0.10 |
IAM, 4% |
0.15 |
Summary
Solvent-based inks used on flexible packaging must be durable and have efficient printing and curing procedures. Dorf Ketal’s Tyzor® IAM titanate is an ideal additive for optimizing solvent-based inks for these properties. It optimizes adhesion to various print layer substrates, promotes quick curing, and increases resistance to abrasion, solvents, and water. Additionally, it has been engineered to mitigate discoloration and odor issues that may result from using other titanate additives. Click below to request a sample of Tyzor® IAM for your ink formulations today.