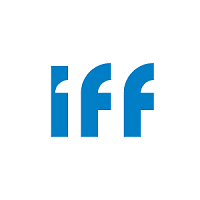 |
Solid chemical and pharmaceutical formulations have been predominant for hundreds of years because they allow for easier storage, handling, transport, and high-active-ingredient loading. While solid formulations are most associated with and used by the pharmaceutical industry today by way of pills and tablets, several other industries are leveraging these formats to gain benefits in convenience and sustainability. |
For example, tablets and granules are commonly used formats for water treatment, disinfection, household cleaning, fertilizer products, and more. In all cases, these solid formulations reduce shipping weight and heftier packaging required to ship their liquid counterparts. Therefore, there has been a recent rise in solid formulations.
While the active ingredient is arguably the most important component of these formulations, binders, also known as excipients, play a critical role in tablet and granule formulations by providing them with the required physical strength and structural form. As more tablet and granule formulations get created, it becomes more important that formulators use the right binders to ensure they achieve the highest product quality and efficiency.
Lattice® NT Microcrystalline Cellulose for Tablets and Granules
Lattice® NT is a microcrystalline cellulose binder developed by IFF for industrial applications to create tablets and granules. For several decades, other IFF microcrystalline cellulose products, such as Avicel®, have been ubiquitous in the pharmaceutical space as an excipient for countless tablet medications.
Lattice® NT microcrystalline cellulose is naturally derived, being made from alpha cellulose content originating from wood pulp. This alpha cellulose is composed of millions of microfibrils that contain paracrystalline and crystalline regions, denoted below as regions A and B, respectively.
The paracrystalline regions are amorphous, flexible cellulose chains, whereas the crystalline regions are rigid, linear cellulose chains. Lattice® NT is obtained by processing and drying the crystalline regions, yielding extremely porous microcrystalline cellulose.
The porosity of the Lattice® NT microcrystalline cellulose structure combined with its high surface area contributes to highly effective usage as a binder and process aid in creating tablets and granules. Additional details on these functionalities are explored below.
Binders and Excipients
Typically, active ingredients are combined with binders and other solid content within the first steps of producing tablets or granules. The key differentiator that makes Lattice® NT a good binder and excipient is its high porosity, which makes it highly compactible. This provides the necessary flexibility to develop tablets with the desired shapes and sizes. Lattice® NT binders also offer increased strength to the tablet, where their high surface area provides much more space for active ingredients and fillers to bind and achieve hydrogen bonding with the cellulose structure. As a result, highly homogeneous and robust tablets are made.
These same properties make Lattice® NT ideal for extruded products, where it functions as a binder, or excipient, to carry formulation components together, providing better shape and homogeneity. Lattice® NT binders also promote rapid and even wetting due to their porosity and high surface area. This is useful in all solid-dose formats to ensure that the active ingredient gets distributed in a homogeneous, controlled manner throughout the liquid phase in which the dose is placed.
Process Aids
Dry granulation and wet granulation are the most common methods used to create granules of a desired size for tablet production. Granulation is done such that the solid ingredients, which begin as powders, gain enough flowability to allow them to be poured easier and measured more accurately into tablet presses. It is also done to increase compaction and achieve active ingredient dispersion within tablets.
In dry granulation, the solid ingredients are mixed and formed into larger aggregates called slugs. These slugs are then forced through a screen to create granules of the desired size. Lattice® NT is useful as a binder here, providing the anticaking properties necessary to prevent granules from sticking together and preventing accurate and efficient compaction.
In wet granulation, which is the preferred method for active ingredients that are not heat sensitive, the solid ingredients are mixed and placed into a fluid bed granulator that gradually introduces a liquid to bind powders together and induce granulation. As more liquid is added to the powder mixture, granules grow larger. However, while finer control over granule size is desirable, it is often difficult to achieve. Usually, the association between liquid volume and granule size is not linear, and there is always a risk of adding too much liquid, turning granules into a slurry.
Lattice® NT is extremely effective as a process aid in wet granulation because its high surface area and large absorptive capacity provide better control over granule size and extend granulation processing windows. Lattice® NT enables liquid to be absorbed at an even rate that correlates strongly with mean granule size, as shown below, allowing the formulators to generally have better control over granule size.
In addition, Lattice® NT widens the processing window for wet granulation by acting as a buffer for water, extending the endpoint at which slurry formation occurs. Below is a chart comparing two formulations, one with Lattice® NT-50 and one without. A torque rheometer was used to assess wet mass consistency. Torque correlates directly with granule size due to increased cohesive strength gained when water is added. As indicated by the graph, more water can be absorbed over a longer period while providing a more gradual change in granule size.
Lattice® NT Grades
Lattice® NT binders and processing aids are available in various average particle sizes, where the ideal option is that which has an average particle size roughly equal to the other solid components in the formulation. Based on specific applications and the ideal corresponding average particle size, there are also general recommendations as a binder or process aid for tablets, extruded products, and granules. While broad, the suggested use level for each grade heavily depends on the concentration of other contents in the formulation.
Application and Function |
Recommended Grade |
Suggested Use Level (%) |
Extruded product binder |
Lattice® NT-50 |
30–80 |
Tablet binder |
Lattice® NT-100
Lattice® NT-200 |
10–60 |
Granulation process aid |
Lattice® NT-20
Lattice® NT-50 |
10–15 |
Industrial tablets and other solid formulations containing Lattice® NT may also benefit from including
Accelerate® DS-813, a cellulose-based dissolution and disintegration aid that significantly decreases the time and mixing required to form solutions in water. More information about Accelerate® DS-813 and the improvements it provides for the dissolution of solid formulations like water-dispersible granules can be found
here.
Summary
Lattice® NT is a naturally derived microcrystalline cellulose binder, also known as an excipient, and process aid essential for creating high-quality, robust solid formulations for a variety of industrial tablet and granule applications. Lattice® NT has highly effective binding capabilities due to its high porosity and surface area, enabling formulation components to coalesce with high strength and homogeneity. Lattice® NT may also be used as a process aid for granulation, allowing for finer granule size control and anticaking properties. Click below to request a sample of a Lattice® NT binder or process aids for your tablet or granule formulation today.