Improve Packaging Film Laminates with Lupasol® P
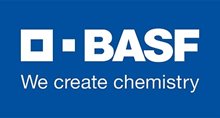 |
|
As manufacturers within food, consumer goods, medical, and other markets strive towards lower cost and sustainability in transporting and storing their goods, traditional rigid packaging such as bottles and cans are being replaced in favor of flexible packaging. This form of packaging, which is lighter in weight and can be transported in tighter volumes than its rigid counterparts, reduces transportation fuel costs and overall consumption of plastic source materials to make the packaging. |
Multilayer Packaging Films
Most flexible packaging manufactured today is made of multilayer films composed of 3-12 layers. Each of these layers provides specific functionality to the packaging, from being a barrier to oxygen and moisture to facilitating print to sealing of the package. These are typically bonded to the adjacent layer with a laminating adhesive or heat-seal coating. Often, the films that make up these layers are made of low surface energy plastics like polyolefins and polyesters, which can be notoriously difficult to adhere to. When plastic film-to-film adhesion for packaging becomes a challenge, pre-treatment is necessary to ensure sufficient bonding.
Film Pretreatment
Plastic films like polyethylene, polypropylene, and PET often undergo oxidative pre-treatment such as the corona plasma process during manufacturing. These oxidative processes initially improve surface energy and make the film more conducive to the surface adhesion of adhesives and coatings. However, this increase in surface energy declines significantly after only a short time during storage. Therefore, an adhesion promoter or primer can be applied to the film to ensure the plastic used in multilayer flexible packaging films continues to accept adhesion towards adhesives and coatings during and after storage.
Lupasol® P - The Ideal Primer for Packaging Films
Lupasol® P is a cationic polyethyleneimine with a branched polymer structure.
It is an incredibly effective adhesion promoter for multilayer packaging films manufactured by coating, laminating, extrusion coating, or coextrusion. The use of
Lupasol® P in multilayer films allows for the combination of materials that improve the physical, chemical, and mechanical properties of the laminate.
Lupasol® P Properties
Usage Recommendations
Lupasol® P should be diluted to 0.5-1.0% in water prior to use. Up to 30 wt% of an alcohol such as methanol, ethanol, or IPA can be added to reduce drying time and improve wettability. Addition of a
nonionic surfactant at 0.5% is also recommended to improve wetting onto low surface energy materials. Lupasol® P primer solutions can be applied at a rate of 1-5 g per square meter using traditional coating methods including dip coating, or transfer roll. Once applied to the substrate, the Lupasol® P primer coating must be throughly dried prior to combination with other films. A warm stream of air can be used to accelerate drying time. Once dried the coated film can be rewound for storage or immediately combined with other films. Combination of the Lupasol® coated film with a topcoat should be carried out under heat (50-100°C) and pressure.
9 ms View Total Time