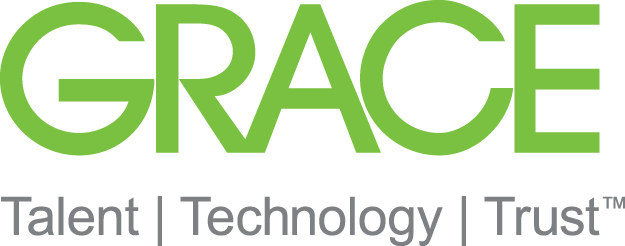 |
|
With cost being top of mind for many companies in the transportation, chemical, and construction industries, long-term corrosion protection of products and assets has become a priority. Various marine, industrial, and architectural structures used by these industries are typically made of steel, which is prone to corrosion when exposed to harsh environments containing high moisture, salt, and chemicals. These types of structures require the long-term anticorrosion protection that zinc-rich primers and coatings provide. |
Zinc-Rich Primers and Coatings
Zinc-rich primer and coating systems are typically applied to steel and protect against corrosion through a couple of mechanisms. First, zinc functions as a physical barrier between steel and its environment, preventing oxygen and moisture from physically contacting the metal underneath that promotes corrosion. However, should oxygen and moisture contact the steel and induce oxidation, zinc then functions as a sacrificial anode that corrodes in place of steel since zinc oxidizes more easily than iron. These mechanisms protect the service life of ships, containers, pipes, machinery, and more against corrosion.
Though zinc is the primary component providing corrosion protection to steel in zinc-rich primers and coatings, a silicate binder is needed to ensure the system forms durable, even films onto the metal substrates they are applied. Therefore, using an optimal binder in zinc-rich primers and coatings is the key to maximizing performance.
Grace Lithium Polysilicate
Grace’s lithium polysilicate is an aqueous, high-ratio silicate solution that serves as the ideal binder for zinc-rich primers and coatings used for anticorrosion applications for several reasons listed below.
- Features a very high silica-to-lithium oxide ratio (4.8)
- Facilitates excellent film formation and provides fast dry times
- Has great compatibility with powdered zinc
- Creates long pot life in zinc-rich systems
Grace’s lithium polysilicate is manufactured with a silica-to-lithium oxide ratio of 4.8, which contains a much higher ratio of silica than other silicate products like sodium or potassium silicate. This is due to the smaller ionic radius of lithium, permitting higher concentrations of silica to be present in solution. Since silica is responsible for binding zinc, lithium polysilicate promotes better film-forming characteristics and faster drying times.
dditionally, Grace’s lithium polysilicate has high compatibility with powdered zinc and provides longer pot life than sodium and potassium silicate. Together, the properties above allow Grace’s lithium polysilicate to create top-performing, zinc-rich primers and coatings with the following features:
- High-impact and abrasion resistance
- Excellent salt-fog and immersion performance
- Rapid cure times
- Broad range of film thicknesses
- Great resistance to chemicals, organic materials, and solvents
- Good compatibility with organic topcoats
In the following sections, starter formulations using Grace’s lithium polysilicate are presented and tested against competitive zinc-rich primer formulations to quantify the increased performance that Grace’s lithium polysilicate provides.
Zinc-Rich Primer and Coating Formulations
|
Zinc Content of Dried Film (%) |
95 |
93 |
93 |
85 |
Component 1 |
|
|
|
|
Lithium polysilicate (parts wt) |
100 |
100 |
100 |
100 |
Potassium dichromate (parts wt) |
0.05 |
0.05 |
0.05 |
0.05 |
Carbopol® suspending agent (parts wt) |
- |
- |
- |
0.4 |
Benagel® or Benaqua® suspending agent (parts wt) |
- |
- |
0.4 |
- |
Component 2 |
|
|
|
|
Zinc powder (parts wt) |
420 |
290 |
290 |
125 |
Properties |
|
|
|
|
Solids (wt film/dry film, vol%) |
72 |
61 |
61 |
41 |
Theoretical coverage at 75 μm film thickness (ft2/gal) |
1150 |
980 |
980 |
660 |
Pot life at 21
°C (hr) |
>48 |
>48 |
>48 |
>48 |
Pot life at 38°C (hr) |
>16 |
>16 |
>16 |
>16 |
Formulation Notes
The formulations above are starting guidelines for zinc-rich primers and coatings, and there are several factors and options that should be considered to provide flexibility and optimal performance. First, the suspending agents listed are by no means the only compatible options; many other types of suspending agents have been found to work. Suspending agents and other additives should not contain high salt concentrations due to the risk of gelling the lithium polysilicate. Next, if desired, pigments such as chrome green oxide, lead oxide, or red iron oxide may also be added to the zinc component in the formulation to provide tinting effects. Finally, zinc dust with particle sizes in the range of 5 to 9 μm is ideal for preventing excessive gassing, early gelation, and reduced pot life, which can lead to poor wetting and cracking at high film thicknesses.
When applying these zinc-rich systems, surfaces should be prepared by removing grease or oil with a solvent. The surface should then be sand-, grit-, or shot-blasted to provide a profile of approximately 25–38 μm. The system may be applied using a spray gun and may be deposited to a dry film thickness of 38–200 μm for optimum performance.
For questions about these formulations and procedures for incorporating these ingredients, please
contact us.
Cure Rates
Zinc-rich primer and coating systems cure into a zinc silicate and polymerized silica matrix when water is removed. Like other water-based systems, zinc-rich primers and coatings cure fastest at higher temperatures and lower humidity. The information below provides guidance pertaining to the approximate timeframe for cure based on various conditions.
Humidity (% RH) |
Temperature (°C) |
Initial Cure (Hours) |
Maximum Dry Abrasion Resistance (Hours) |
Topcoat Readiness (Hours) |
Absolute Cure (Hours) |
40–60 |
10–32 |
0.75 |
2.0 |
12.0 |
30.0 |
20–50 |
32–52 |
0.33 |
0.5 |
2.0 |
3.5 |
2–10 |
1.00 |
5.0 |
20.0 |
78.0 |
50–90 |
32–52 |
0.33 |
1.0 |
2.5 |
4.0 |
2–10 |
3.00 |
10.0 |
36.0 |
144.0 |
Zinc-Rich Primer and Coating Properties and Performance
The formulation detailed above containing 93% zinc content was evaluated against competitive primer systems for film properties and performance. The results below indicate that the primer using Grace’s lithium polysilicate exhibited excellent hardness, great cathodic protection, high abrasion resistance, and good stability when immersed in water, brine, or jet fuel and when exposed to salt spray.
Property |
93% Zinc- Content Primer |
Competitive Primer A |
Competitive Primer B |
Competitive Primer C |
Competitive Primer D |
Pencil hardness after 12 days |
H |
H |
5-B |
5-H |
H |
Abrasion resistance, indexa |
1.0 |
1.0 |
14.4 |
0.9 |
8.3 |
Immersion performanceb |
S |
S |
S |
S |
S |
Cathodic protectionc |
+ |
G |
+ |
G |
G |
5% Salt-fog test, 2000 hrc,d |
+ |
G |
G |
G |
− |
a Index established through film weight loss (mg/1000 cycles) when abraded with Taber Abraser fitted with CS-17 wheels, loaded with 500 g each. Smaller numbers indicate lower weight loss and higher abrasion resistance
b ”S” indicates satisfactory performance of coating after being immersed in tap water, brine, and jet fuel
c ”G” indicates good performance, “+” indicates superior performance, and “-“ indicates poor performance
d Refers to Federal Test Method 141-6061
Field test panels were prepared and coated with the 93% zinc-rich primer formulation to be compared against the competitive primer systems. The panels were exposed to 24 months of testing in several types of environments, including marine atmospheres, marine tidal zones, a steel mill, and industrial salt and acid sites. In all cases, the primers formulated with lithium polysilicate outperformed each competitive primer system in terms of providing surface protection.
|
Ratings After 24-Month Exposure without Topcoat |
Test station |
93% Zinc- Content Primer |
Competitive Primer A |
Competitive Primer B |
Competitive Primer C |
Competitive Primer D |
Marine atmosphere |
8 |
8 |
8 |
5 |
5 |
Marine tidal zone |
8 |
7 |
2 |
4 |
2 |
Steel mill |
8 |
7 |
5 |
2 |
3 |
Industrial salt site |
5 |
3 |
1 |
1 |
2 |
Industrial acid site |
5 |
6 |
7 |
1 |
6 |
Average |
6.6 |
6.2 |
4.6 |
2.6 |
3.6 |
1 = Compete failure of coat, 2 = Poor performance (plane failure), 3 = Poor-to-fair performance, 4 = Fair performance (incipient plane failure), 5 = Fair-to-good performance, 6 = Good performance (edge failure), 7 = Good-to-excellent performance, 8 = Excellent performance (no failure)
Test panels were also prepared in the same fashion as above but with the application of a polyamide–epoxy topcoat. The results below indicate that the 93% zinc-rich primer again outperformed competitive primers.
|
Ratings After 24-Month Exposure with Polyamide–Epoxy Topcoat |
Test station |
93% Zinc- Content Primer |
Competitive Primer A |
Competitive Primer B |
Competitive Primer C |
Competitive Primer D |
Marine atmosphere |
8 |
7 |
2 |
4 |
2 |
Marine tidal zone |
7 |
7 |
5 |
2 |
3 |
Steel mill |
5 |
4 |
4 |
1 |
3 |
Industrial salt site |
5 |
4 |
4 |
1 |
3 |
Industrial acid site |
7 |
8 |
4 |
6 |
6 |
Average |
6.8 |
6.5 |
3.8 |
3.3 |
3.5 |
1 = Compete failure of coat, 2 = Poor performance (plane failure), 3 = Poor-to-fair performance, 4 = Fair performance (incipient plane failure), 5 = Fair-to-good performance, 6 = Good performance (edge failure), 7 = Good-to-excellent performance, 8 = Excellent performance (no failure)
Summary
As companies in the transportation, chemical, and construction industries tighten their budgets, corrosion protection for assets and products made of metal becomes increasingly important. Grace’s
lithium polysilicate is the ideal binder for zinc-rich primers and coatings for lasting protection against salt, moisture, and chemicals due to its high silica-to-lithium oxide ratio, allowing it to form films with high durability and fast cure rates. Zinc-rich primers and coating formulated using the guidelines contained in this article outperform competitive systems. Click below to request a sample of Grace’s lithium polysilicate today, and we will be glad to assist you in your formulation efforts.